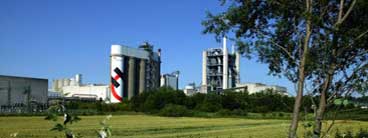
WHAT CONSUMERS
SHOULD KNOW ABOUT CEMENT
An individual planning to build a house of his own or a builder goes to the market to buy cement for the construction work. Cement is freely available in the market under different types, grades and brand names. Each type and grade cater to the specific requirement of the construction. Many times consumers do not have the full knowledge of these aspects. Besides the cost, the quality of cement is important from the point of view of strength and durability. Some technical aspects about cement, which every consumer building a house buying from a builder would like to know, are explained in the following paragraphs.
Cement varieties: Some common types of cement available off-the-shelf in the market are ordinary Portland cement (OPC) in grades 53, 43 and 33;
Using cement at site: Using cement at site requires conformation to certain requirements as specified by the relevant Standards. At site, cement is used as mortar (cement+sand) or concrete (cement+sand+aggregate). It is necessary that all the ingredients are mixed properly and in right proportion, mortar/concrete is transported and properly placed and compacted at the construction site and adequately cured. Control on the addition of water (water/cement ratio) is of particular importance. It will be difficult to obtain full benefit from the cement quality, if any of these processes are not carried out properly. Consult your structural engineer on that.
Meaning of the Grade of cement in Indian Standard: The Grade refers to the minimum 28-day compressive strength in MPa, measured according to the standard procedure.Thus 43 Grade cement refers to the standard compressive strength of 43 MPa or 430 kg/sq.cm., at 28 days. Remember that the Grade of cement is only one of the criteria deciding the quality of construction. The desired strength and durability of structure can be ensured only by following good construction practices at the site, as mentioned earlier.
Durability of construction: The structure is called durable when it gives satisfactory, economic, service life over the period for which it is designed. The durable structure has sufficient resistance towards internal and external agents causing corrosion of reinforcement, expansion of concrete due to sulphate attack, alkali-silica reaction and carbonation and deterioration due to freeze and thaw cycles. One major factor contributing to the durability is the permeability of concrete. In general, lesser the permeability, better is the durability.
Test certificate: When you buy cement, ask for the lated test certificate supplied by the cement manufacturer. The test report normally contains values of soundness for free lime and magnesia, setting time, compressive strength (3, 7, 28-day), loss on ignition, insoluble residue, chloride and alkali content. Check these values against those specified by the Standard. The standard values are given in the report itself, in most cases. The meaning of some important tests is as follows:
(i) Soundness: Indicates the extent of expansion that the cement may undergo after setting. Cement with lower expansion is preferred.
(ii) Setting time: The 'Initial Setting Time' indicates the duration within which the concrete is workable and should be placed. The 'Final Setting Time' is the upper limit of time beyond which the concrete shall loose its plasticity and shall begin to harden.
(iii) Compressive Strength: The compressive strength at 28 days indicates the capacity of cement to bear compressive load. The strength at 3 and 7 days is important from the point of view of removal of structural supports and scaffoldings. It should be noted that it is the strength of concrete which is important at the site. Hence the design and control of the concrete mix and construction practice are important.
(iv) Loss on Ignition (LOI): The excess LOI indicates some kind of adulteration or partial setting of cement during storage.
(v) Insoluble Residue (IR): The excess IR is an indication of adulteration
(vi) Chloride and Alkalies: A good quality cement should have lower values of chloride and alkalies, than the upper limits specified by the IS Code, from the durability considerations
(vii) Ideal color of cement: There is no ideal color of cement. It depends upon the chemical composition and the additive materials (fly ash, blast furnace slag) blended with cement during the process of manufacturing. A good quality cement may have a greenish, gray, brownish or blackish color. However color of cement does not affect its physical or chemical properties.